Kamis, 01 September 2016
Contoh Kata Pengantar
15.05.00
No comments
KATA PENGANTAR
Puji dan syukur penulis
ucapkan kehadirat Allah SWT, yang telah memberikan rahmat dan hidayah-Nya
sehingga penulis dapat menyelesaikan penulisan Tugas Akhir ini, Selawat beriring
salam penulis sanjung sajikan ke pangkuan alam nabi besar Muhammad SAW, yang
telah membawa umatnya dari alam kebodohan ke alam yang penuh dengan ilmu
pengetahuan seperti yang kita rasakan saat ini.
Pada penulisan Tugas
Akhir ini penulis mengambil judul “Rancang
Bangun Mesin Penghancur Buah Coklat” Maksud dan tujuan penulisan Tugas Akhir ini
adalah sebagai salah satu syarat untuk Dapat memperoleh gelar Diploma IV di
Politeknik Negeri Lhokseumawe.
Dalam penulisan Tugas Akhir ini banyak
kendala yang penulis alami, namun berkat bantuan dari berbagai pihak, maka Tugas
Akhir ini dapat penulis selesaikan tepat pada waktunya, Untuk itu penulis
mengucapkan terima kasih kepada :
1.
Bapak
Ir.Nahar, MT selaku Direktur Politeknik Negeri
Lhokseumawe.
2.
Bapak
Ir. H. Saifuddin, MT Selaku Ketua Jurusan
Teknik Mesin Politeknik Negeri Lhokseumawe, sekaligus Pembimbing Utama dalam penyelesaian Tugas Akhir ini.
3.
Bapak Sumardi, ST, MT Selaku Pembimbing Utama dalam penyelesaian Tugas Akhir ini.
4.
Bapak Ir. Sariyusda, ST, MT Selaku Pembimbing Pembantu dalam penyelesaian Tugas Akhir ini.
5.
Bapak
Ir. Mawardi, ST, MT Selaku Ketua Program Studi Jurusan Teknik
Mesin Politeknik Negeri Lhokseumawe.
6.
Seluruh
Staf Pengajar Jurusan Teknik Mesin Politeknik Negeri
Lhokseumawe.
7.
Ayahanda
dan ibunda serta keluarga yang telah memberikan segalanya demi mencapai dan menggapai
masa depan penulis.
8.
Seluruh
rekan-rekan Mahasiswa mesin yang telah banyak membantu penulis dalam
menyelesaikan tugas ini.
Penulis menyadari bahwa dalam
penulisan Tugas Akhir ini, masih banyak terdapat kesalahan dan kelemahannya,
maka dengan ini penulis siap menerima saran dan kritikan yang sifatnya
membangun demi kesempurnaan tulisan ini dimasa yang akan datang.
Semoga tulisan ini dapat
bermanfaat bagi pembaca sekalian terutama kepada penulis sendiri. dan semoga
Allah SWT senantiasa membimbing kita ke jalan yang diridhai-Nya. Amin.
Lhokseumawe,
19 April 2016
Penulis
M Nurhubaizah Haris
Nim : 1221301020
DAFTAR ISI
Hal
LEMBARAN JUDUL
LEMBARAN PENGESAHAN
KATA PENGANTAR ...................................................................................... i
DAFTAR ISI ..................................................................................................... iii
DAFTAR GAMBAR ....................................................................................... vi
DAFTAR
TABEL............................................................................................ vii
BAB I PENDAHULUAN.......................................................................... 1
1.1 Latar Belakang................................................................................... 1
1.2 Tujuan Penulisan................................................................................ 2
1.2.1
Tujuan Umum.................................................................................. 2
1.2.2
Tujuan Khusus................................................................................. 2
1.3 Alasan
Pemilihan Judul..................................................................... 2
1.4
Pembatasan Masalah........................................................................ 3
1.5 Metode Pengumpulan Data............................................................... 3
1.6 Rumusan Masalah............................................................................. 3
BAB II TINJAUAN PUSTAKA................................................................ 4
2.1 Tanaman Coklat (Kakao).................................................................. 4
2.1.1 Buah Coklat.................................................................................. 4
2.1.2 Cara Pengupas.............................................................................. 5
2.2 Pengertian Mesin Penghancur Buah Coklat...................................... 5
2.3 Komponen yang Digunakan.............................................................. 6
2.3.1 Poros............................................................................................. 6
2.3.2 Pasak............................................................................................. 9
2.3.3 Bantalan....................................................................................... 10
2.3.4 Puli............................................................................................... 11
2.3.5 Sabuk........................................................................................... 11
2.3.6 Baut dan Mur.............................................................................. 13
2.3.7 Motor Bensin............................................................................... 13
2.4 Material Kontruksi Mesin................................................................. 14
2.5 Proses Permesinan............................................................................ 14
2.5.1 Proses Pengelasan (las listrik)...................................................... 15
2.5.2 Proses Gerinda............................................................................. 16
BAB III METODE PRODUKSI.............................................................. 17
3.1 Tempat dan Waktu........................................................................... 17
3.2 Konsep Kerja Mesin......................................................................... 17
3.2.1 Parameter Proses Permesinan...................................................... 17
3.2.2 Dimensi Mesin............................................................................. 18
33 Proses Pembentukan......................................................................... 20
3.3.1 Hoper (Saluran Masuk)................................................................ 20
3.3.2 Cesing.......................................................................................... 20
3.3.3 Rangka......................................................................................... 21
3.3.4 Tabung Pemecah.......................................................................... 21
3.3.5 Saluran Keluar............................................................................. 22
3.4 Fungsi Dari Masing-masing Komponen........................................... 22
3.4 Diagram Alir (flow chart)
proses pembuatan.............................. 23
DAFTAR PUSTAKA
LAMPIRAN
DAFTAR GAMBAR
Hal
Gambar 2.1 Buah Coklat.....................................................................................
5
Gambar 2.2 Mengupas buah
coklat manual ........................................................ 5
Gambar 2.3 Macam - macam bantalan............................................................... 10
Gambar 2.4 Konstruksi Dan Ukuran Penampang Sabuk-V................................ 12
Gambar 2.5 Motor Bensin................................................................................... 14
Gambar 3.1 Desain mesin penghancur buah
coklat............................................. 18
Gambar 3.2 Pandangan....................................................................................... 19
Gambar 3.3 Potongan A-A ,
B-B........................................................................ 19
Gambar 3.4 Hoper (Saluran
Masuk).................................................................... 20
Gambar 3.5 Cesing.............................................................................................. 20
Gambar 3.6 Tabung Pemecah (mata penghancur)............................................... 21
Gambar 3.7 Rangka............................................................................................. 21
Gambar 3.8 Saluran Keluar................................................................................. 22
Gambar 3.9 Diagram Alir Tahapan Kegiatan...................................................... 23
DAFTAR TABEL
Tabel 2.1 Klarifikasi
proses permesinan menurut jenis mesin perkakas yang digunakan 15
Tabel 3.1 Rancangan
Fungsional......................................................................... 35
Kamis, 12 Desember 2013
Motor Injeksi
11.41.00
No comments
Mengenal Sistem Injeksi Sepeda Motor di Indonesia yang seperti telah kita ketahui bahwa motor yang memiliki sistem injeksi mulai dikenalkan pada sekitar tahun 2005. Namun respon konsumen akan motor injeksi masih kurang karena masyarakat lebih senang membeli motor dengan sistem karburator dibanding memilih sepeda motor sistem injeksi karena jika terjadi kerusakan lebih mudah diperbaiki sendiri. Pada awal tahun lalu progres penjualan motor injeksi sudah meningkat dan semakin banyak produsen motor seperti yamaha, honda kawasaki, suzuki dan merek terkenal lainnya yang memproduksi motor dengan menggunakan sistem Injeksi pada tahun ini.
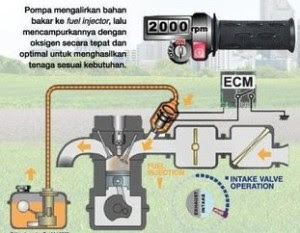
Lalu sebenarnya apa sih Kelebihan dan Kekurangan motor sistem Injeksi ini ?
Berikut melalui gambar-modifikasi-motor-terbarus memberikan informasi mengenai Kelebihan dan Kekurangan motor sistem Injeksi :
Kelebihan Motor Injeksi
1. Campuran udara dan bensin selalu akurat (perbandingan ideal) pada semua tingkat putaran mesin.
Pada motor injeksi, volume penyemprotan bensin selalu akurat karena dikontrol oleh ECU sesuai dengan masukan sensor-sensor yang bertebaran di sekujur mesin. Seperti sensor rpm, jumlah udara masuk, posisi katup gas hingga kondisi cuaca di sekitar mesin.
Bahkan pada kondisi pengendaraan tertentu seperti percepatan, deselerasi dan beban tinggi, ECU mampu mengontrol perbandingan bensin dan udara tetap ideal. Kondisi ini memberikan keuntungan tersendiri yaitu mengurangi emisi gas buang dan lebih hemat pemakaian bensin.
2. Hemat bahan bakar
Campuran udara dan bahan bakar di mesin injeksi yang selalu akurat, membuat penggunana bahan bakar menjadi lebih efisien alias hemat.
3. Tarikan lebih responsif
Pada tipe karburator, antara pengabut bensin (spuyer) dengan silinder jaraknya agak jauh. Selain itu, perbedaan bobot berat jenis antara bensin dan udara mengakibatkan volume udara yang masuk tidak imbang dengan jumlah bensin yang dihisap. Sehingga tarikan menjadi kurang responsif.
Sedangkan motor injeksi menempatkan pengabut bensin (injektor) dekat silinder. Saluran bensin yang menuju injektor bertekanan antara 2,5 s/d 3,0 kg/cm2 lebih tinggi dari tekanan intake manifold. Berhubung diameter mulut injektor sangat kecil, ketika sinyal listrik dari ECU mengaktifkan injektor maka bensin yang menyembur berbentuk kabut.
Saat katup gas dibuka, udara dan bensin menghasilkan campuran yang homogen serta perbandingan yang ideal. Dibantu mutu api yang bagus akan menghasilkan pembakaran sempurna. Hasilnya tarikan lebih responsif sesuai perubahan katup gas.
4. Mesin mudah dihidupkan tanpa dipengaruhi perubahan kondisi cuaca
Pada temperatur rendah (dingin), menghidupkan mesin berkarburator dibutuhkan campuran lebih gemuk dengan menarik cuk. Cara manual ini tak lagi diperlukan pada motor injeksi karena sudah dilengkapi sensor temperatur mesin serta sensor temperatur udara masuk. Saat menghidupkan mesin (starting) dan kondisi dingin, secara otomatis jumlah semprotan bensin ditambah. Sehingga mesin mudah dihidupkan dalam kondisi apapun dan tidak terpengaruh kondisi cuaca.
5. Perawatan mudah
Jika karbu ketika dibersihkan harus dibongkar sehingga membutuhkan waktu lama, belum lagi resiko karena sering dibongkar sehingga beberapa komponen jadi rentan aus,terutama skep pelampung. sedang untuk tipe motor yang menggunakan injeksi rentan waktu perawatan lebih lama, cukup 10-15 ribu kilometer sekali, itu pun cukup di semprotkan injector cleaner. bahkan jika kualitas bengsin yang digunakan bagus, sebenarnya injeksi tidak perlu diapa-apakan lagi. karena selain steril, juga telah dibackup dengan filter halus sebelum masuk ke injector biar lebih aman.
6. Ramah lingkungan
Karena terjadi pembakaran sempurna pada ruang bakar, sehingga emisi gas buang yang di hasilkan relatif lebih sedikit apalagi knalpot dilengkapi catalic converter. Di knalpot motor injeksi biasanya di lengkapi catalytics converter (CC), sistem ini akan merubah zat zat hasil pembakaran yang berbahaya menjadi zat yang lebih ramah ligkungan atau dengan menggunakan sistem sensor O2.
Tidak memerlukan cuk lagi. Karena pada motor injeksi ada sensor temperatur yang akan melaporkan suhu mesin ke ECM yang akan memerintahkan injektor untuk memperkaya campuran bensin pada suhu mesin dingin.
7. Daya lebih besar
Karena konstruksi nosel/injektor tepat pada intake manifold sehingga campuran bahan bakar lebih homogen.
8. Waktu servis lebih cepat.
Karena fuel injection tehnologi berkonsep bebas perawatan, sehingga pada saat servis motor yang di bersihkan cuma pada bagian filter udara, busi dan setel klep.
Kekurangan Motor Injeksi
1. Perawatan Harus di Bengkel Khusus
Karena motor injeksi tidak bisa di utak atik secara sembarangan, maka perawatan atau perbaikan harus di lakukan pada bengkel resmi.
2. Modifikasi lebih mahal
Bagi anda yang suka modifikasi motor, anda harus mengeluarkan dana lebih jika ingin memodifikasi motor injeksi.
3. Harga sparepart lebih mahal
Sparepart atau sukucadang motor injeksi terbilang cukup mahal. Motor injeksi juga butuh alternator atau pembangkit listrik lebih besar.
4. Lebih sensitif soal kelistrikan
Kerusakan kecil pada kelistrikan dapat mengakibatkan motor mati.
5. Sensitif terhadap kualitas bahan bakar
Karena mulut injektor sangat kecil sehingga sangat sensitif terhadap kualitas bahan bakar. Oleh karena itu disarankan menggunakan pertamax sebagai bahan bakar motor injeksi. Selain itu, kerja catalytics converter juga di pengaruhi kadar timbal dalam bahan bakar.
Semoga Ber ManfaaT Bagi Anda Dan jangan Lupa Like Ya
Semoga Ber ManfaaT Bagi Anda Dan jangan Lupa Like Ya
Contoh Laporan Balancing
11.17.00
2 comments
Contoh Laporan Balancing
https://www.paypal.me/MenejerMEDAN?ppid=PPC000654&cnac=ID&rsta=id_ID%28id_ID%29&cust=WRMQN8WRDURZU&unptid=38acf220-7086-11e7-96b1-8cdcd4b6ee30&t=&cal=a7a1f8ea174f6&calc=a7a1f8ea174f6&calf=a7a1f8ea174f6&unp_tpcid=ppme-social-business-profile-created&page=main:email&pgrp=main:email&e=op&mchn=em&s=ci&mail=sys
BAB I
PENDAHULUAN
1.1
Latar
Belakang
Pengujian balancing adalah pengujian yang dilakukan untuk menentukan
dimana letak titik-titik ketidakseimbangan yang terdapat pada suatu rotor yang
bulat sempurna.
Pada laporan ini yang dibahas hanyalah tentang pengujian balacing
terhadap batu gerinda pedestal. Batu gerinda ini digunakan untuk menggerinda
suatu bahan yang memiliki tingkat toleransi yang sangat kecil.
Batu gerinda pedestal yang
dihasilkan oleh pabrik memiliki bagian-bagian yang tidak seimbang (unbalance)
yang disebabkan oleh ketidaksamaan distribusi massa sistem poros batu gerinda terhadap
sumbu putar yang pada umumnya terjadi
pada saat pabrik memproduksinya. Ketidaksamaan distribusi massa ini terjadi pada saat percetakan dimana
terdapatnya kekosongan-kekosongan ataupun menumpuknya bahan dasar batu gerinda
pada suatu sisi. Untuk mengurangi ketidakseimbangan yang terjadi pada batu
gerinda tersebut, dipasanglah beberapa badul yang berfungsi untuk
menyeimbangkan putaran batu gerinda. Penyeimbangan ini dapat dilakukan dengan
menggeser-geser bandul tersebut.
1.2
Tujuan
percobaan
Secara garis besar
pengujian Balancing ini dilakukan dengan tujuan :
a.
Mempelajari jenis-jenis Unbalance
b.
Mempelajari Penyebab terjadinya Unbalance
c.
Mempelajari dimana letak titik-titik Unbalance
d.
Mempelajari cara-cara membalanckan suatu rotor yang
Unbalance
BAB II
TEORI DASAR
2.1 Balancing
Balancing
didefinisikan sebagai kesamaan distribusu massa
sistem poros rotor terhadap sumbu putar.
Kondisi
balance akan terjadi bila memenuhi persyaratan :
Σ Fx = 0
Σ Fy = 0
Σ M = 0
Kondisi tidak
balance pada suatu sistem poros rotor yang berputar disebabkan adanya gaya inersia ( Fi
)
Fi
= m.R. ω 2
dimana
: Fi = gaya inersia ( gaya
sentrifugal )
m = massa
tak balance ( W/g )
R =
jarak titik pusat putaran denga titik pusat tak balance
ω =
kecepatan sudut sistem poros rotor yang berputar
Sistem poros
rotor tunggal
Sistem poros
rotor tunggal adalah satu poros yang mempunyai satu lempengan.
Adanya gaya Fi pada
poros tersebut akan mengakibatkan :
1.
terjadi deformasi pada poros tersebut yang berbentuk
melengkungnya poros
2.
bila Fi terlalu besar akan mengakibatkan
poros patah
3.
meleengkungnya poros akan memberikan dampak yang serius
terhadap komponen-komponen lain seperti, rusaknya bantalan, seal dan
sebagainya.
4.
terjadi getaran pada frekuensi 1x kecepatan putar
5.
terjadi gesekan antara komponen yang berputar dengan
casing
6.
terjadinya fatique
7.
suara semakin berisik
Dalam kenyataannya ( pada sistem poros rotor yang terdapat pada turbin,
kompresor, pompa ), rotor hampir selalu tidak merupakan sistem rotor poros
tunggal, dam tempat masssa penyeimbang tidak terletak pada lempengan yang
bersangkutan. Umumnya disediakan tempat khusus untuk tempat massa penyeimbang.
Couple adalah
dua gaya yang sama besarnya, bekerja pada arah
yang berlawanan dan antara gaya
mempunyai jarak.
Besarnya kopel
adalah :

dimana
: K = Kopel ( Nm )
F = Gaya ( N )
L = Jarak antara dua gaya (
m )
Untuk melakukan
penyeimbangan pada suatu bidang dapat dilakukan dengan kaidah :
Σ Fx = 0
Σ Fy = 0
Σ M = 0
Σ WR
cos θ = 0 kesetimbangan gaya-gaya
arah horizontal
Σ WR
sin θ = 0 kesetimbangan gaya-gaya
arah vertikal
Σ WR a
cos θ = 0 kesetimbangan momen pada
bidang A terhadap gaya
horizontal
Σ WR a
sin θ = 0 kesetimbangan momen pada
bidang A terhadap gaya
vertikal
2.2 Unbalance
Unbalance didefinisikan sebagai
ketidaksamaan distribusi massa
sistem poros rotor terhadap sumbu putar. Definisi lain menyatakan bahwa
unbalance adalah kondisi tidak berimpitnya sumbu putar poros dengan sumbu
principal.
Sumbu principal
adalah sumbu dimana massa
sistem poros rotor terdistribusi merata pada sumbu tersebut.
Unbalance yang
berlebihan menyebabkan getaran pada rotor dan struktur penyangga-nya. Kondisi
ini akan memperpendek umur mesin.
Formulasi
unbalance :


dimana
: F =
gaya
(newton)
m = massa (kg)
R = jari-jari (meter)
2.3 Jenis-jenis
Unbalance
Jenis unbalance dapat dapat digolongkan
berdasar hubungan geometrik antara sumbu poros dan sumbu principal (principal
axis).
2.3.1
Statik
Unbalance
Statik unbalance adalah suatu kondisi
unbalance dimana sumbu principal bergeser terhadap sumbu poros. Unbalance
disebut juga unbalance gaya
(force unbalance) atau unbalance kinetic.

Gambar 1. Static Unbalance
Static unbalance dapat dideteksi dengan
menggunakan knife edge. Sistem poros rotor akan berputar sedemikian rupa
sehingga titik terberatnya dibawah.
Cara yang lain
untuk mendeteksi adalah dengan menggunakan pendulum. Massa unbalance akan terletak pada posisi paling bawah.
2.3.2
Couple
unbalance
Couple unbalance adalah kondisi dimana
principal axis memotong sumbu poros pada center gravitinya. Unbalance ini
terjadi jika massa
unbalance terletak pada jarak yang sama terhadap ujung poros, mempunyai berat
sama tapi berlawanan arah.

Gambar
2. Couple unbalance
Couple unbalance
disebut juga moment unbalance. Untuk mengetahui adanya couple unbalance dapat
digunakan metode dinamik. Jika sistem poros berputar maka akan terjadi getaran
yang berbeda fasa 180° pada dua bidang.
2.3.3
Quasi static
unbalance
Sangat
jarang suatu sistem poros rotor mempunyai tipe unbalance static atau couple
murni. Normalnya kondisi yang terjadi adalah campuran antara keduanya. Sumbu
poros dan sumbu principal masing-masing berpotongan tetapi bukan pada center
gravity. Kondisi ini disebut Quasi Static unbalance.

Gambar 3. Quasi Statik Unbalance
Quasi unbalance
akan terlihat mempunyai getaran yang berbeda besarnya dan ber-lawanan arah pada
dua bidang.
2.3.4
Dynamik
unbalance
Dynamik unbalance sangat sering
terjadi. Kondisi ini terjadi jika sumbu principal dan sumbu poros tidak
berpotongan dan tidak parallel. Unbalance jenis ini mempunyai getaran yang
besar dan fasa berbeda tetapi bukan 180°.

Gambar
4. Dynamik Unbalance
2.4 Penyebab Unbalance
o
Blow holes
pada pengecoran. Impeller pompa atau pulley yang besar kadang-kadang
mempunyai blow holes atau pasir yang terjebak yang disebabkan karena proses
pengecoran
o
Eccentricity.
Terjadi jika geometric centerline tidak berimpit dengan rotating centerline.
Contohnya adalah jika suatu rotor bulat sempurna tetapi pusat putarnya tidak
pada center.
o
Key and
Keyways. Jika pembuat pulley membalance pulleynya tanpa key, dan pembuat
motor membalance motor juga tanpa key, maka ketika komponen ini digabungkan key
yang dipasang akan menyebabkan unbalance.
o
Distorsi.
Walaupun komponen sudah sudah dianggap pada kondisi balance pada proses
pembuatannya, pada proses selanjutnya mungkin saja tarjadi distorsi yang
menyebabkan terjadinya perubahan bentuk dari komponen tersebut.
Thermal distorsion adalah distorsi yang disebabkan oleh
tidak meratanya perubahan bentuk yang disebabkan oleh temperatur. Hamper semua
metal memuai jika dipanaskan. Jika pemanasannya tidak merata, maka perubahan
bentuk juga tidak merata yang akhirnya akan menyebabkan kondisi unbalance.
o
Clearance
tolerance. Salah satu penyebab unbalance yang sangat umum adalah akumulasi
toleransi yang berakibat terjadinya pergeseran ukuran.
o
Korosi dan
keausan. Komponen yang bekerja pada lingkungan korosif atau mudah terjadi
keausan sedemikian rupa sehingga terjadi korosi dan keausan yang tidak merata
akan menyebabkan kondisi unbalance.
o
Deposit
built-up. Rotor yang digunakan
dalam menangani proses pemindaha material mengalami unbalance yang disebabkan
oleh menumpuknya material secara merata.
BAB III
METODE PENELITIAN
3.1
Tempat dan
waktu
Praktikum dilaksanakan di lab.
Maintenance Teknik Mesin
Pertemuan pertama pada tanggal November 2013
Pertemuan kedua pada
tanggal November 2013
Pertemuan ketiga pada
tanggal November 2013
3.2
Metode
balancing
3.2.1
Persiapan
Ada beberapa hal yang perlu
diperhatikan sebelum melakukan praktikum balancing. Hal-hal tersebut adalah :
a.
Cek vibrasi dan analisis dengan hati-hati sehingga
menghasilkan kesimpulan bahwa getaran tersebut disebabkan benar-benar oleh
terjadinya unbalance. Analisis yang salah akan membuat proses balancing menjadi
sia-sia karena getaran masih tetap besar.
b.
Lakukan inspeksi pada motor atau poros-poros jika ada
kemungkinan-kemung-kinan retak. Yakinkan bahwa semua baut terikat dengan benar.
c.
Cek rotor terhadap adanya tumpukan kotoran.
d.
Dari data analisis, catat manakah arah radial
(horizontal-vertikal) yang menunjuk-kan nilai lebih besar. Tempat sensor pada
arah pembacaan yang benar.
e.
Sebelum melakukan rekaman data unbalance, yakinkan
bahwa mesin sudah berjalan kontinu. Banyak mesin dari kondisi diam kekondisi
stabil operasinya memerlukan waktu.
3.3
Prosedur
Balancing
- Peralatan praktikum
Adapun alat-alat yang digunakan pada praktikum ini adalah :
a.
Batu gerinda pedestal
b.
Bandul
c.
Busur derajat
d.
Spidol
permanen
e.
Kunci L 8 mm
- Langkah-langkah praktikum
Adapun langkah - langkah dalam melakukan praktikum ini adalah :
a.
Memeriksa kondisi peralatan.
b.
Assembly peralatan.
c.
Mencari titik-titik balance.
d.
Mengukur
jarak antara bandul
BAB IV
ANALISA DATA
Berdasarkan hasil penelitian yaitu
mencari titik-titik unbalance, maka telah ditemukan titik-titik dimana bandul
itu diletakkan yaitu sebagai berikut :
Bandul 1
= 180°
Bandul 2
= 85°
Bandul 3
= 75°
Jarak Antara Bandul 1 ke bandul 2 = 85°
Jarak Antara Bandul 2 ke bandul 3 =
155°
Jarak Antara Bandul 3 ke bandul 1 =
80°
BAB V
KESIMPULAN DAN SARAN
5.1 Kesimpulan
Berdasarkan hasil dari praktikum pada Laboratorium Maintenance dapat
diambil beberapa kesimpulan yaitu :
a.
Bahwa setiap batu gerinda pedestal yang dibuat oleh
pabrik masih terdapat titik-titik unbalance.
b.
Untuk menyeimbangkan suatu batu gerinda pedestal,
dipasanglah beberapa bandul yang dapat diatur dengan mengeser-geser bandul
tersebut.
c.
Tidak samanya jarak antara titik unbalance yang satu
dengan yang lain menye-babkan tidak sama juga jarak antara bandul yang satu
dengan yang lain.
5.2 Saran - saran
a.
Sebaiknya pada saat pelaksanaan praktikum, para
mahasiswa lebih memper-hatikan tahap-tahap pelaksanaan praktikum agar
telaksananya praktikum tersebut seperti yang diharapkan.
b.
Mahasiswa sebaiknya lebih disiplin dalam mengikuti
praktikum.
DAFTAR PUSTAKA
Rotor Balancing & Shaft Alignment,
PT. Wahana Ilmu Sarana Hakiki.